So you’ve got a project that needs to look great. Tight tolerances and incredible precision are on your mind. We bet the potential cost is riding your brain waves, too.
Perhaps you’ve already opted to go with sheet metal laser cutting instead of plasma or waterjet cutting -- or perhaps an older, cheaper process. Chances are you're frantically trying to pin down a price, just like the little guy in the photo.
Here’s what you can expect with sheet metal laser cutting services in terms of cost -- both short- and long-term.
Sheet Metal Laser Cutting Costs: How Do They Compare?
Laser cutting is certainly more cost-effective than using hand tools to cut metal. And despite being a high-end process that costs more than plasma cutting, it’s still cheaper than waterjet cutting. Mechanical or machine cutting processes tend to be cheaper. Many quality manufacturers offer a combination of machine and laser cutting services so you can choose the best fit for your project.
How does laser compare with plasma? The answer depends.
Laser cutting offers a lower cost for material about 12 gauge and thinner, while the advantage for punch plasma cutting increases as your material of choice gets thicker. At the heaviest metal thickness (more on this in a bit), punch plasma holds a 40% cost advantage over laser. In this scenario, precision plasma cutting has a higher cost than both.
What Else Goes into Laser Cutting Costs?
As with most manufacturing, there are a variety of factors that go into to the total cost of laser cutting services:
- Equipment and labor costs
- Production costs
- Long-term maintenance and viability of laser cutting
1. Equipment and Labor
The main reason you’re paying more for laser cutting is the cost of the technology. A laser cutting machine is probably setting back the manufacturer at least $200,000. Depending on size, power, and sheet-handling capacity, that number can skyrocket past $500,000.
Thankfully, lasers have a low overall tooling cost. The gases we use to produce the laser are inexpensive, and increased demand has driven down component costs. Nonetheless, peripheral equipment -- think gold mirrors or zinc selenide windows and lenses -- can add expenses.
As far as operating costs, you’re in luck. It's more common for fabrication companies to allow a laser cutter operator to perform secondary operations or to run additional machines than with other cutting processes. More efficiency equals more finished product and a lower overall cost for you.
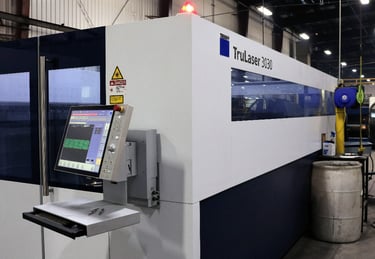
2. Production
Sheet metal laser cutting prices range from $13 to $20 an hour in manufacturer costs alone. Typically a laser cutting manufacturer pays 65% to 85% of the production cost of waterjet services.
The most expensive part of this production process is all the power it needs to convert electricity into light. You’re best to leave this to a metal manufacturing company and not try it at home, folks.
When assessing what laser services will cost you, here’s the question that affects you most: What you are cutting?
Every machines has a limit of what level of thickness and, perhaps, material type it can handle. The more resilient the machine, the more you’ll pay to reap its benefits. Notably, when cutting sheet metal, lasers don't handle thick stuff very well, so their cost-effectiveness loses steam in those applications.
Sometimes the metal, or even the grade of metal, plays a part in how effective the laser will be. Just look at stainless steel alone:
- Austenitic stainless steel is one of the most commonly used steels in the construction industry. You can harden austenitic grades without the use of heat, yet it retains awesome strength. This makes austenitic stainless ideal for laser cutting technology.
- Ferritic stainless steel includes chromium and carbon. This steel works extremely well with thinner sections with smaller or no welds. This means it's plenty suitable for laser cutting.
- Martensitic stainless steel is similar to ferritic stainless steel -- lots of chromium and carbon here. An engineer can temper and harden martensitic stainless. This magnetic group of metals is often used in applications requiring sheet and plate metal.
- Duplex stainless steel is a combination of ferritic and austenitic. It's higher-strength than either one by its lonesome. This steel type behaves well when cut by laser.
No matter the material, when a manufacturer starts the process, laser metal cutting's blazing speed plus pinpoint precision obviously make it more efficient than waterjet. How obvious?
- It takes 16 seconds for a laser to cut through a ⅛” sheet.
- It takes 75 seconds for a waterjet to cut through a ⅛” sheet.
Quicker work results in less money spent on labor and electricity.
After the laser cut is complete, there’s little to no cleanup to be done. A small amount of dust is all that results, and that’s easily removed with vacuuming and filtering, so you won’t be paying to facilitate special disposal of waste like what’s produced with waterjet cutting.
3. Long-Term Maintenance and Viability
Lasers don't dull, so there's no pause during manufacturing to switch out tooling. And additional tooling replacement costs just don’t exist. What’s this all mean? You’ll have a new product in your hands no time.
We will say this: Laser use is technically demanding. If you don’t find a good servicer, you may end up later on with components that need replacement or repair.
So here’s another question to ask yourself: Can you justify the price of going laser by profiting long-term from the fruits of your provider’s labor?
Need Top Quality? Try Laser
Though it might be more expensive than some other styles we’ve mentioned, laser technology’s precision and versatility are unmatched. So If you have a project that requires very tight tolerances and clean cuts, the cost of laser cut sheet metal should not be a deterrent should be at the top of your list -- just remember that you're paying for quality!
(Editor's note: This article was originally published in July 2017 and was recently updated.)